Ensuring a Safe and Efficient Pharmaceutical Manufacturing Process with APS
Ensuring safety and efficiency in pharmaceutical manufacturing is paramount due to the nature of the products involved. Tablets, pills, and capsules often contain Active Pharmaceutical Ingredients, which can generate harmful dust and high solvent concentrations during handling and manufacturing processes. To safeguard employee health and prevent cross-contamination of products, implementing effective dust and fume extraction systems, combined with containment solutions, is essential.
Before we cover how we can help, it’s crucial to comprehend the intricacies of the manufacturing process. Typical applications include tablet pressing, coating, fluid bed drying, spray drying, blending, and granulation. Handled ingredients encompass powders, granular substances, Active Pharmaceutical Ingredients, and solvents. This means conducting a comprehensive risk assessment for each application is vital, to determine the appropriate extraction solution.
Industry challenges
When handling pharmaceutical dust, attention must be focused on three critical areas. First and foremost is the protection of workers from exposure to potent, toxic, or allergenic dusts.
This requires the implementation of robust safety measures including where airborne dust pose a significant threat to product quality and compliance with regulatory agencies.
Stringent controls and monitoring systems are imperative to prevent contamination and maintain adherence to regulatory standards. Furthermore, the trend toward smaller Active Pharmaceutical Ingredient molecules and increased solvent usage exacerbates these challenges, necessitating solutions to ensure safe and compliant pharmaceutical dust handling practices.
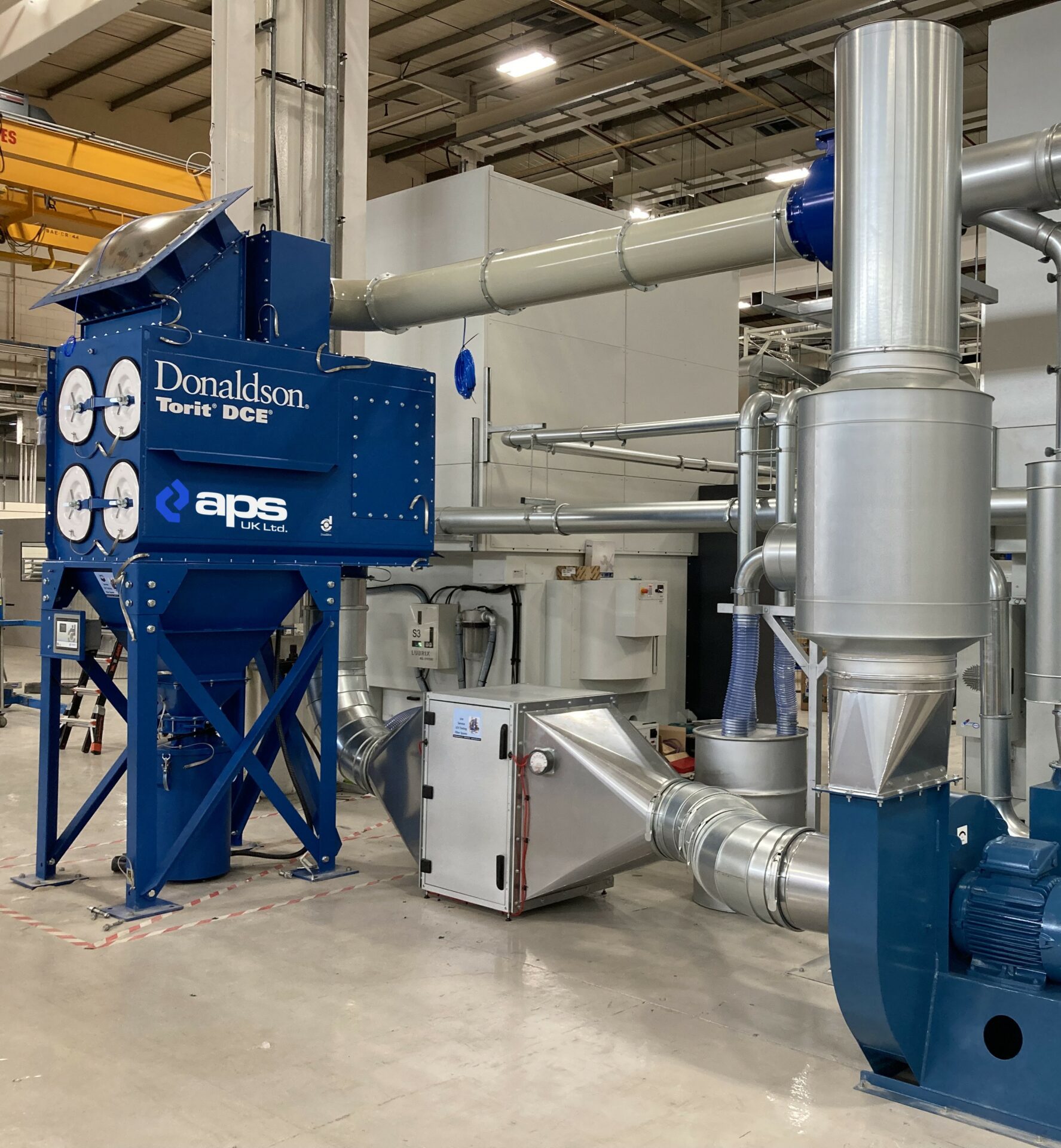
How our dust extraction systems can help
Our dust extraction systems offer tailored solutions to address the needs of pharmaceutical processes effectively. Extracting residual airborne dust at the source is prioritised to prevent workplace contamination.
Sizing the dust collector appropriately enables efficient handling of airflow and dust concentrations, while effective containment of potent dusts throughout the extraction and maintenance processes is maintained.
Our systems also provide the features to change out spent filters safely. Given the dust could contain toxic particles, the filter change out can require a Bag-In/Bag-out process. This process involves bags which are connected to integrated collars on the collector. The bags are attached to the collars using rubber gaskets and band clamps to create a dust-tight seal between the BIBO collars on the collector.
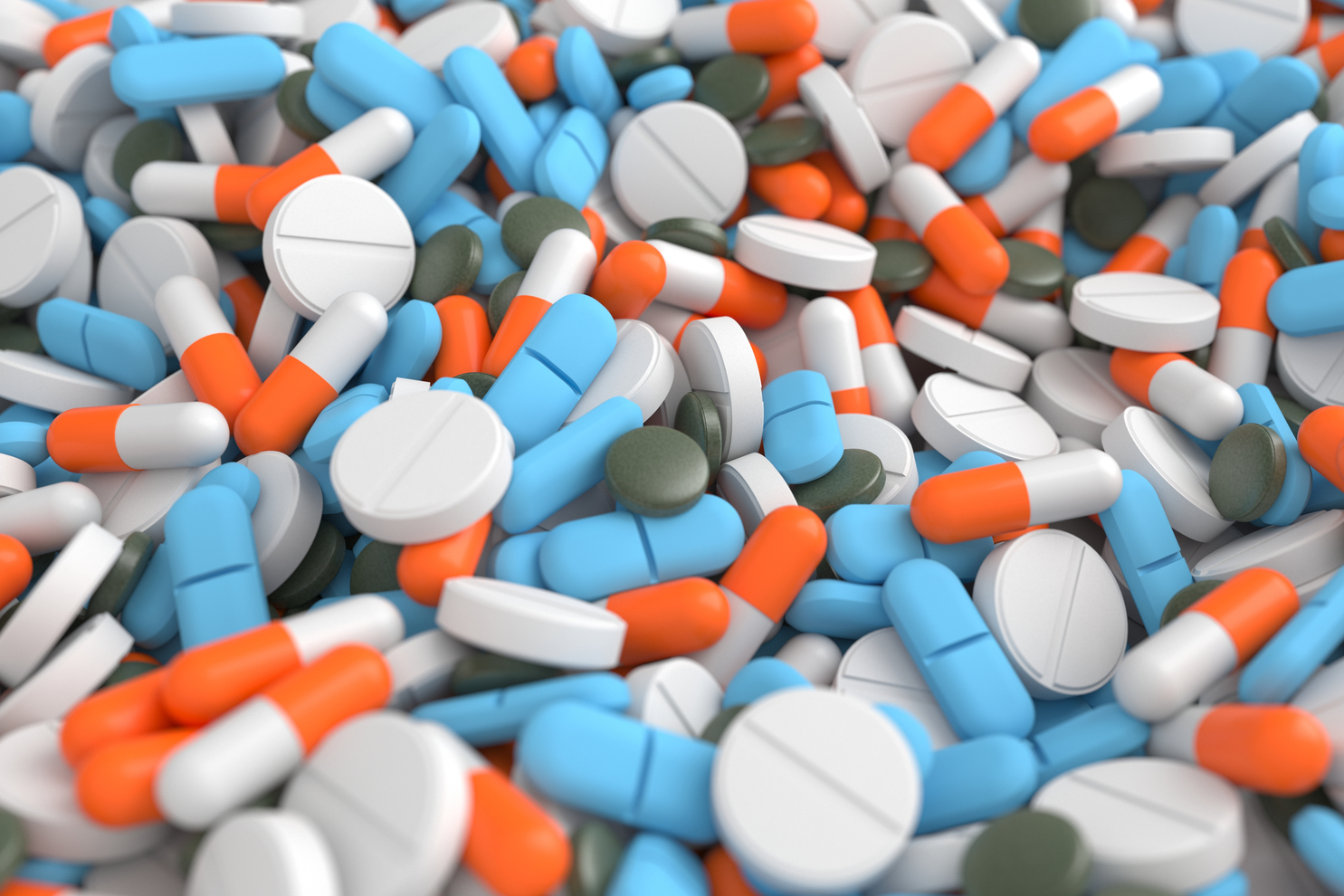
Benefits to your business
Through implementing our dust extraction systems, your business can ensure adherence to strict regulatory standards governing manufacturing such as the COSHH ACOP L5 & Health and Safety at Work Act. Our solutions mitigate the risk of contamination and help maintain product quality, facilitating compliance with COSHH regulations.
Our systems efficiently eliminate harmful dust and fumes at their source, significantly reducing employee exposure to potentially hazardous substances. The consequences of inhaling dust particles are profound, as they can lead to various respiratory issues and even permeate the bloodstream. The severity of health effects depends on factors such as particle size, type, and duration of exposure. Larger particles tend to lodge in the upper respiratory tract, causing damage, while fine particles easily infiltrate the lungs, resulting in more severe health complications. Moreover, dust ingestion can provoke gastrointestinal infections or systemic effects by entering the bloodstream, affecting other organs.
Our dust extraction systems also optimise the manufacturing process by efficiently handling airflow and dust concentrations at the machinery, thereby enhancing productivity, and reducing downtime. Effective containment of potent dusts throughout extraction and maintenance processes ensures seamless operations, minimising disruptions, and maximising throughput. Additionally, features such as easy filter change-out streamline maintenance procedures, further boosting operational efficiency.
Do you need help improving the safety and efficiency of your pharmaceutical manufacturing process? Contact us today.
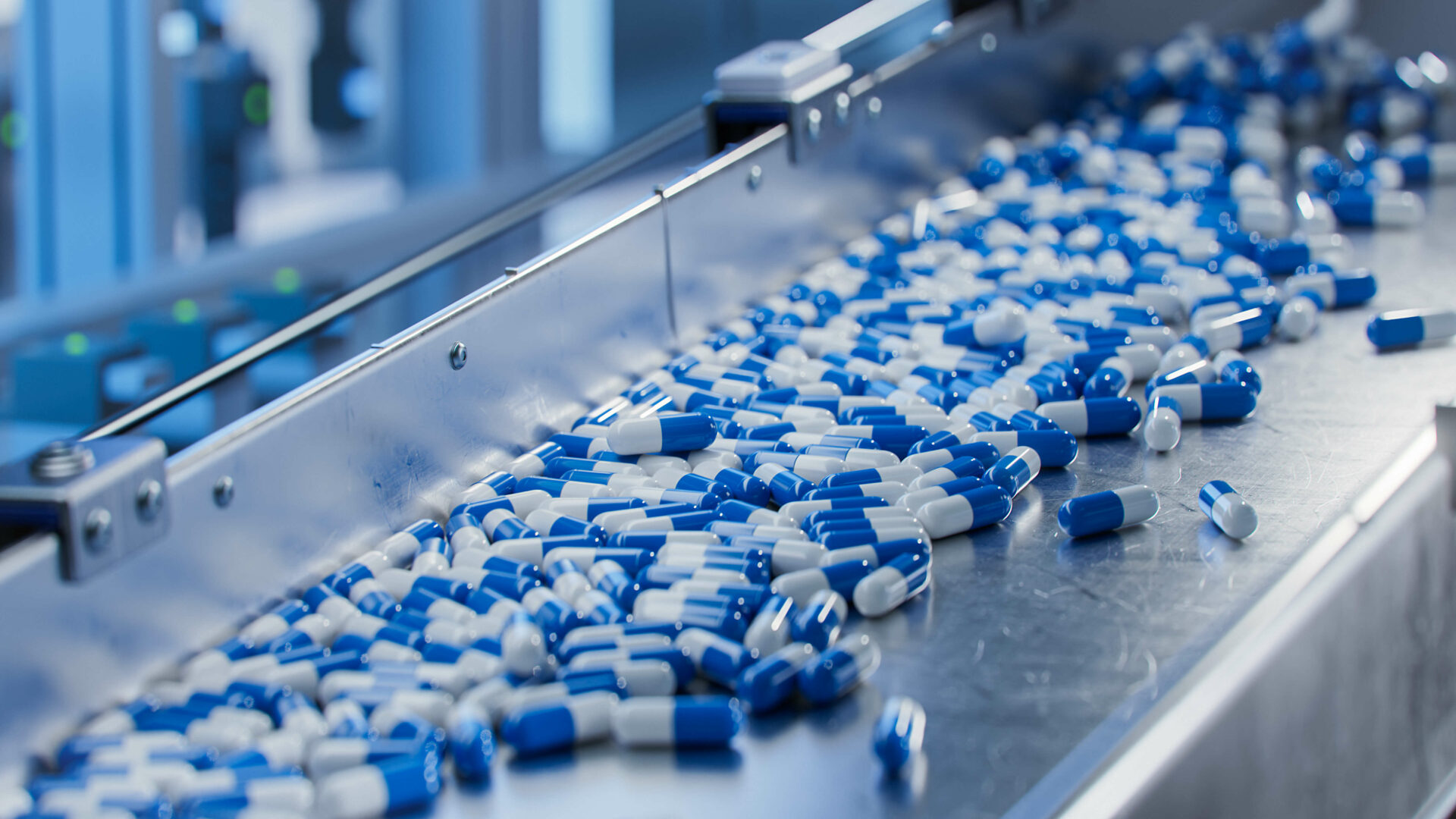
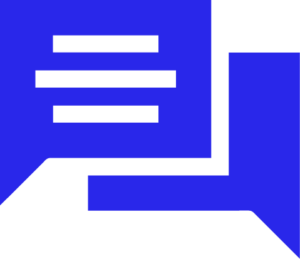
We Consult
Understanding is key. We take the time to grasp your specific requirements, ensuring solutions tailored just for you.
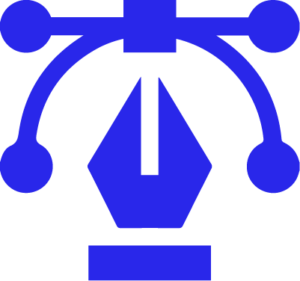
We Design
With your needs as our blueprint, we craft designs that are both functional and in step with modern aesthetics.
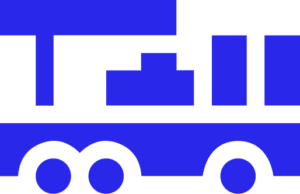
We Install
Our team prioritises a smooth, efficient installation process, minimising disruption while focusing on optimal safety outcomes.