The Critical Role of Dust Extraction in Pharmaceutical Manufacturing
The pharmaceutical industry is renowned for its strict hygiene and cleanliness requirements. However, the industrial processes involved can generate harmful dusts, which can cause potential risk to workers. To avoid breaking workplace regulations, and ensure the health of their employees is protected, it’s therefore important for pharmaceutical companies to install efficient dust extraction solutions.
What are the most common types of dust contaminants in pharmaceutical manufacturing?
Dust can be generated during the production and packaging processes in pharmaceutical manufacturing plants. These processes include tablet pressing, tablet coating, blending, fluid-bed drying, and granulation, and involve handling granular ingredients, including powders, solvents, and active pharmaceutical ingredients (API).
Exposure to some substances, including steroids, hormones, and antibiotics can have adverse effects on workers, causing cumulative damage over time. Health risks faced from exposure to dust include respiratory illnesses, skin reactions, and the potential of developing cancer.
How can I prevent cross-contamination between different products in my pharmaceutical manufacturing facility?
Beyond risks to worker health, pharmaceutical companies also have a duty to prevent cross-contamination, to stop those who consume their products coming into harm.
While pharmaceutical manufacturing facilities do have high levels of cleanliness, this is something which needs to be actively maintained, often taking up lots of time, money, and staffing resources. This is where dust extraction systems can provide the answer.
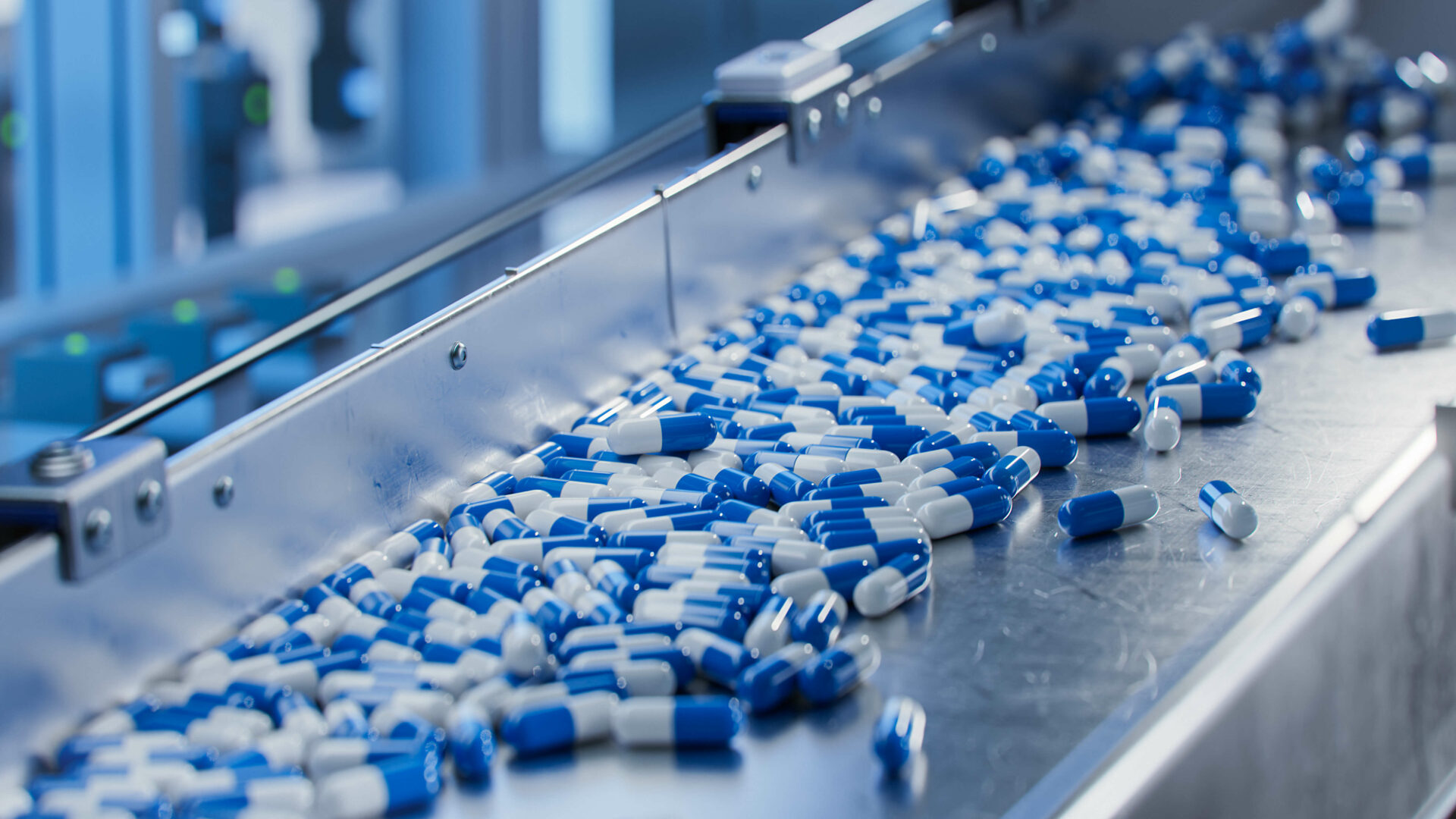
At APS, we offer tailored solutions to effectively address the needs of pharmaceutical companies. We can install dust control systems which extract airborne dust at source, preventing cross-contamination between products. It’s important to size the dust collector appropriately, to enable efficient handling of airflow and dust concentrations, whilst remaining effective in containing potent dust throughout the extraction process.
To aid with the cleaning and maintenance of dust extraction systems in pharmaceutical facilities, our systems provide the features to change out spent filters safely.
As the dust handled within pharmaceutical processes can involve toxic particles, we offer a Bag-In/Bag-out process for filter changes. This process involves bags which are connected to integrated collars on the collector, using rubber gaskets and band clamps to create a dust-tight seal.
These processes help to prevent cross-contamination within the workplace, helping your pharmaceutical manufacturing business maintain the high-quality of its products.
What are the latest regulations regarding dust control in pharmaceutical manufacturing?
To avoid hefty fines and lengthy legal cases, it’s vital that pharmaceutical manufacturers ensure they comply with industry standards.
In the UK, the Control of Substances Hazardous to Health (COSHH) regulations require employers to prevent or reduce their workers’ exposure to substances that are hazardous to their health. Meanwhile, the Good Manufacturing Practices (GMP) is the minimum standard that a medicines manufacturing must meet in their production processes and ensures that medicinal products are consistently produced and controlled to the quality standards appropriate to their intended use.
At APS, we will conduct an extensive risk assessment, looking at the applications your business uses, and the types of dust generated, and determining the most appropriate dust extraction solution for you. Through implementing our dust extraction systems, your business can ensure adherence to the strict regulatory standards set by COSHH and GMP, mitigating the risk of contamination, and protecting the health of your employees.
Are you looking to implement dust extraction systems in your pharmaceutical manufacturing environment? Get in touch with us today, to find out how we can provide a bespoke solution that suits your needs.
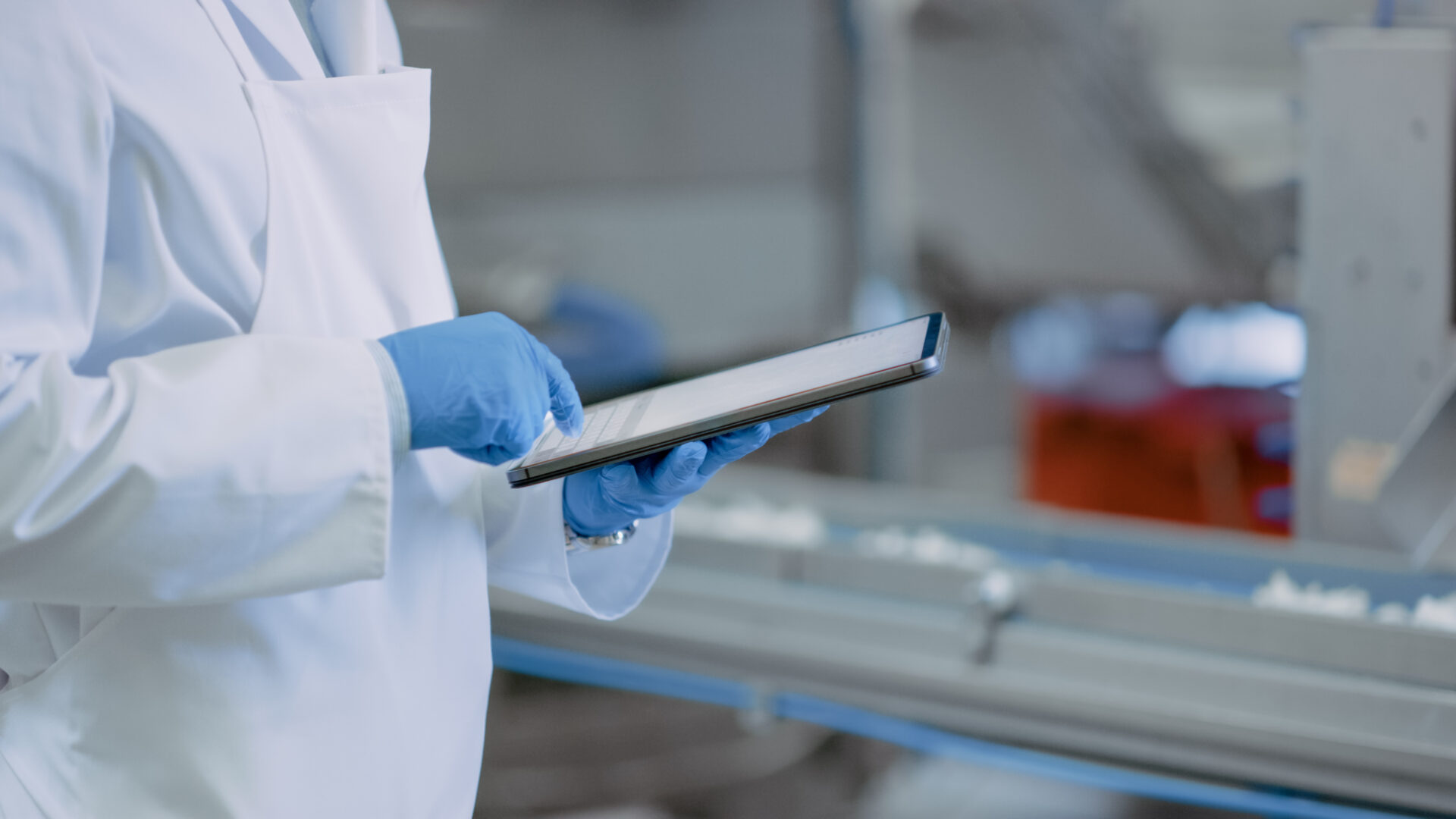
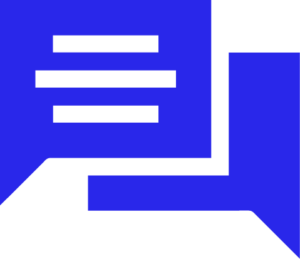
We Consult
Understanding is key. We take the time to grasp your specific requirements, ensuring solutions tailored just for you.
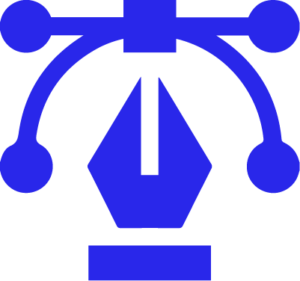
We Design
With your needs as our blueprint, we craft designs that are both functional and in step with modern aesthetics.
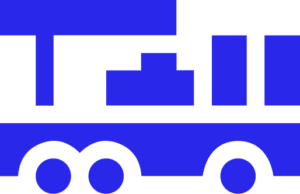
We Install
Our team prioritises a smooth, efficient installation process, minimising disruption while focusing on optimal safety outcomes.